Introduction
There are three pillars of every high-quality CNC yield – “Precision, Accuracy, and Tolerance.” Most CNC machine experts talk endlessly about delivering the highest precision, accuracy, and tolerance through their ‘state-of-the-art’ technologies. But it’s nothing other than a marketing gimmick. Frankly speaking, behind every high-quality CNC machining service is sound knowledge and understanding of machining fundamentals and concepts.
To help you have a firm grasp over CNC machining, we will get down to the nitty-gritty of CNC milling machine accuracy, tolerance, and precision. The information in the post will help you better define your product design requirements and manufacture without feeling overwhelmed. Let’s get started!
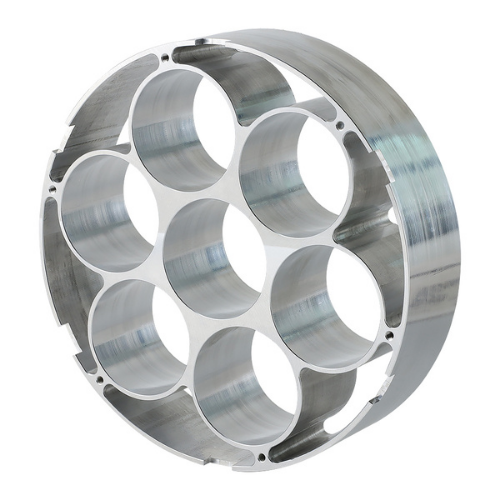
What is accuracy
Accuracy is keeping the degree of conformance to a known standard or value. Seems confusing? Let us understand it in depth. A highly accurate CNC machine, set to cut a piece of metal 100mm long, should cut the metal to exactly 100mm. In other words, there should be no error. The more accurate the CNC machine will be, the easier it will be to get exactly 100mm.
The term ‘accuracy’ can be defined as follows:
“The degree to which a measurement or movement in space conforms to a systematic standard or one of its derivatives – typically the millimeter or micron for metric measurements.”
However, accuracy isn’t inherent to the CNC machine. You will have to understand and learn how to use the machine well. After all, some machines are more accurate, and some are less. But, to achieve the best result, you will have to set up and run the machine in a certain way. So, how should you improve your CNC machine accuracy? Here are some of the best practices you can employ and achieve accurate product design.
1.Know the spindle
It is crucial to know the spindle’s behavior. You might want to treat the tool-tip position as static, but varying speeds create different temperatures and centrifugal forces within the spindle. As a result, the spindle responds and fails to hold tighter tolerances. We suggest you conduct adequate experimentation to identify the tool-tip position. This helps apply tool offsets to make appropriate corrections.
2.Identify potential error sources
Although inspection happens after the machining process is over, we suggest you measure and inspect first to identify the sources of errors. This gives you a chance to correct the measurements before machining. What can be the potential sources of error? A machining center (three-axis) has 21 potential sources of inaccuracy. Simply identifying the potential error sources will help reduce the need for gaging.
3.Don’t ignore the drawbar
The drawbar delivers the holding force required to keep the spindle in place. Therefore, one should inspect the drawbar routinely. Reviewing the drawbar condition once every month keeps the machine’s accuracy in check. A weak drawbar will not only increase the probability of error but also significantly reduce the tool life. One should expect the drawbar repair and approach it periodically.
4.Reduce the chatter
A loose setup and tooling often result in chatter. Chatter can be put in check using diagnostic tools. Such tools overcome chatter by finding a spindle speed at which the rate of cutting edge impacts harmonizes with the system’s natural frequency. You should also engage in test cutting to find the ideal spindle speeds. This will help achieve a quieter cut and better accuracy. It also helps achieve a higher metal removal rate.
5.Check performance with a reference
You can use a known reference object inside the machining zone to inspect the CNC machine’s performance. Make sure the reference object is made from the same material and has similar geometry. The reference object will allow you to capture any measurement error and calculate the difference between the known value of a reference dimension and the measured value of that same dimension. You can use the difference as an offset and achieve better accuracy.
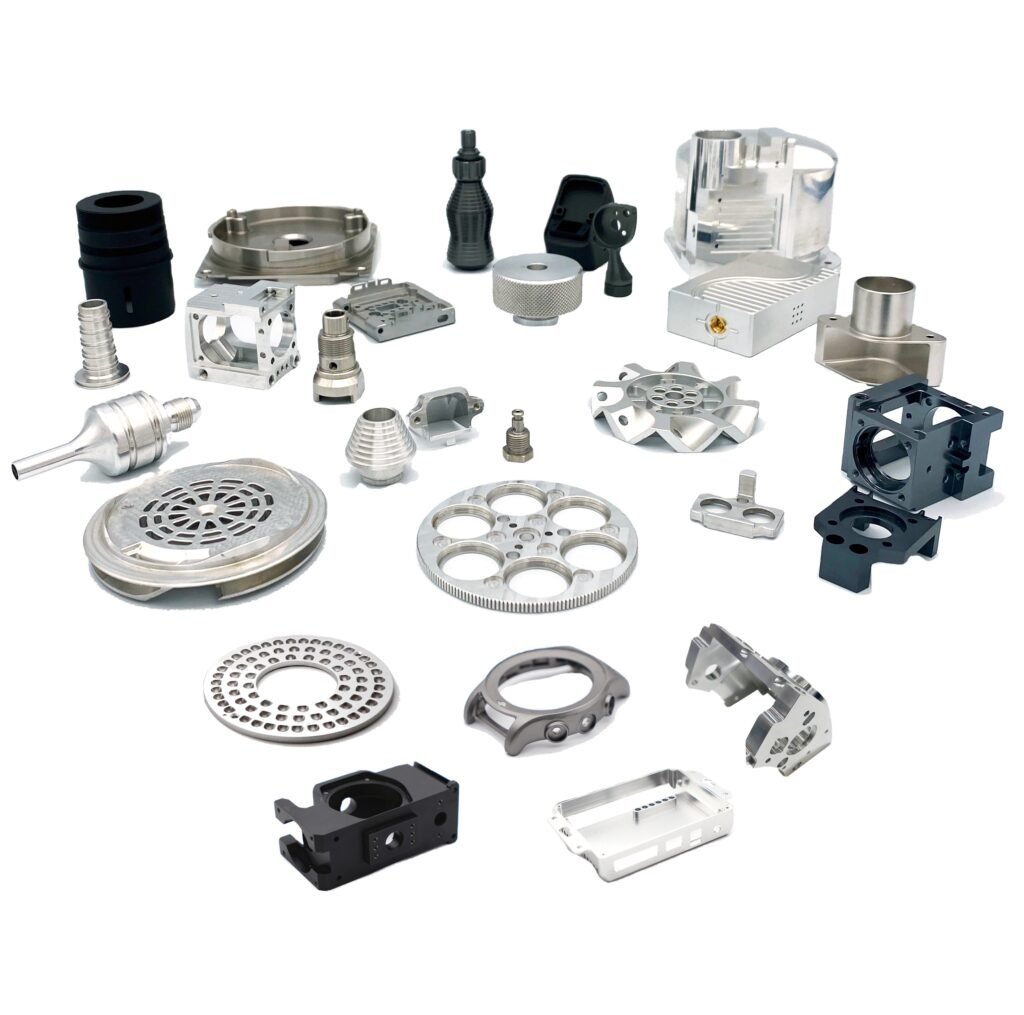
What is precision?
When it comes to using CAD software to design a product, the result is often a precise one. It’s because the software is designed to reliably produce/repeat any design feature. Such software reduces labor and saves time. However, things change dramatically once you take the drawing to a factory.
Precision during CNC machining refers to the machine’s ability to repeat an action every time without producing a random error. In other words, precision machining involves controlling the process without deviating from the process or measurement. Accuracy and precision are used interchangeably. But, both are quite different. Let’s discuss how we can achieve precision in CNC machining.
1.Use good CNC programming skills
The most basic task in CNC machining is CNC programming. You will need an experienced programmer that can write a flexible intrinsic program while reducing the cumulative error of the CNC system. The programmer should be able to leverage the relationship between the main program and subroutines. This helps improve processing efficiency and consistency.
2.Adjust the processing system
One should adjust the blade extension according to the workpiece material and then perform a trial cutting. Machining experts often use this method for single-piece small batch production. It will be easier to achieve precision if you adjust the relative positions of the machine tool, workpiece, and fixture.
3.Reduce the measurement errors
Measurement errors will increase the probability of a bad product design. Therefore, you should aim to prove the machining accuracy of the box support hole and spindle shaft journal. Routinely measure and adjust the radial runout range of the corresponding part to reduce measurement errors.
4.Measure and adjust parts with bearing
CNC machining requires the parts with bearing to be accurate. The rotation accuracy of the bearing is crucial for the CNC machine to perform correctly. Therefore, you should strive to improve the rotation accuracy by selecting cylindrical roller bearings, multi-oil wedge bearings, and hydrostatic bearings.
5.Keep machining tools in good condition
Make sure you keep all the machining tools in prime shape and condition. Routinely indulge in tool regrinding as it helps extend the tools’ life. You can also purchase special cutting oil to maintain sufficient lubrication in the CNC machine. Most importantly, choose the correct lathe tools during the machining process.
6.Reduce thermal error
The thermal error occurs due to the thermal deformation of the processing system. Such errors depend on various factors like cutting speed, feed, machining time, and environmental temperature. Focusing on the factors and tips mentioned above will help improve precision during CNC machining.
What is the difference between accuracy and precision?
Now that we have discussed accuracy and precision in detail, can you tell the difference between the two? Do the differences even matter if both accuracy and precision are used interchangeably? Let’s find out.
Let’s assume we are throwing darts to hit the bullseye on a target practice chart. Accuracy, in this situation, will mean ‘how close’ the dart is to the center of the chart (10 points). Let’s say you hit to achieve 9 points. This means you were 90 percent accurate with your shot.
Now, you decided to hit a seven-pointer thrice. If you succeed, you will be 70 percent accurate. However, you’d have achieved more precision. In other words, precision refers to the repeatability of a certain outcome.
Let’s understand precision and accuracy in terms of manufacturing. Let’s say you need to make a 50mm x 50mm x 50mm cavity in a copper workpiece. A highly accurate CNC machine will deliver a piece of exactly 50mm x 50mm x 50mm measurement. A highly precise CNC machine will deliver this exact same cut for multiple units.

What is tolerance?
The last measurement concept you need to learn is tolerance. CNC machining comes with an allowable deviation that is accompanied by a value. You will find CNC machine shops claiming their machining tool can achieve a tolerance of some value. This is important to note since the machining operation might introduce a deviation of up to 0.05mm in the units.
For example, let’s say you need to create a 10mm hole in a copper workpiece. A CNC machine with a tolerance of 0.05mm might create a hole with a diameter ranging between 9.95mm and 10.05mm. Tolerance is a crucial factor that can impact your design’s functionality. Therefore, we suggest you learn how to achieve small tolerances in a design.
Firstly, you should know that not all parts require tight tolerances. We suggest you consider the function of your part before determining the degree of accuracy required. Parts that don’t interact with other working parts don’t require high accuracy. Achieving tight tolerance is a costly affair. So, we wouldn’t recommend it for parts that don’t need such high accuracy.
Secondly, one should only go for reputable CNC machinists. Only an experienced manufacturing expert will understand your goals and specifications. Subsequently, the expert will share the best tolerances for your project. However, CNC machining services will automatically work with the standard (±0.005 inches) tolerance. Such small deviations are not noticeable to the naked eye.
1.Use quality CNC machines
You should not compromise the quality of CNC machines or workshops. It is virtually impossible to achieve the desired tolerance in a trembling workshop. Check the CNC machines. If you work on a machine with a tolerance of ±0.02mm, how can you guarantee a ±0.01mm tolerance? A workman is as good as his tools.
2.Set the right temperature
The workshop temperature also matters when making precise parts. Temperatures within a workshop can vary by more than 10 degrees between day and night. Therefore, you can’t expect a consistent tolerance while working on the metal with such significant temperature variation. Make sure you work on the project in a workshop with air conditioning.
3.Get the tool holder balance right
Tool holders in the CNC machine should have a dynamic balance. Unbalance will eliminate accurate machining. Without balance, the CNC machine will experience misalignment, asymmetrical rotor design, concentricity errors, and other errors resulting in less accurate parts. You should use a professional balancing service if the holders aren’t designed for easy adjustments.
4.Use correct sharp cutting tools
We suggest you use high-quality and sharp cutting tools for parts that require high tolerances. Dull cutting tools will wear out your CNC machine and reduce the part’s accuracy and precision. This is because the dull tool has a larger radius, making it difficult to make shallow cuts. Take good care of the tools and keep them in proper condition.
5.Performance on-machine inspection
Inspect the finished parts as part of quality control. This helps guarantee tight tolerances. We recommend using an on-machine inspection system that keeps the machine’s accuracy in check. Renishaw inspection systems are one of the best on-machine inspection systems available in the market. These provide automatic offset correction.
Keep reading!
There you have it. This extensive guide focused on breaking down concepts of accuracy, precision, and tolerance with respect to CNC machining. To summarize what you have just read, ‘accuracy’ is achieving a design that is close to the standard; ‘precision’ is achieving accuracy over and over again; ‘tolerance’ is keeping variability to a small and acceptable degree. We hope that now you can define your product design requirements to any CNC machining expert without confusion. Did you find this post helpful? Let us know in the comments. Also, don’t forget to check out other informative posts on the blog!