Electronics enclosure accomplishes two specific goals, safety and aesthetics. While enclosures are commonly used to keep electronics safe, they keep the user safe from electrical accidents. Enclosures come in various shapes, sizes, and materials. Choosing suitable material and size options for your electronics enclosure can be complicated.
So, to help you in your enclosure manufacturing journey, we have broken down this complex topic into easily digestible bits.
Here is an in-depth guide to the best options for your electronics enclosure.
What is an Enclosure?
Enclosures are outer casings designed to contain, protect and organize electronics. Most electronic enclosures are made of metal for added strength, but some prefer plastic as a cost-saving measure.
The three core elements of any enclosure manufacturing are as follows.
- Manufacturing Process
- Material Choice
- Enclosure Design
A firm grasp of these three elements will help you design and manufacture a successful electronics enclosure.
Electronics Enclosure Manufacturing
Manufacturing is the first and foremost important element of enclosure design. Numerous manufacturing techniques are commercially available for enclosures.
- CNC Machining
CNC machining is an incredibly versatile means of production. Here a computer-controlled cutting tool removes material from a block (workpiece) until the desired shape is achieved.
You can machine complex designs with excellent tolerances using CNC. Additionally, you can use almost any material with a CNC machine, as long as you have the necessary cutting tool.
CNC machining is ideal for early prototypes and quick turnarounds. But this versatility comes at a cost. CNC machining can prove to be very expensive for large-scale productions.
- Sheet Metal Fabrication
Sheet metal fabrication involves bending, cutting, and forming 2D sheets of metals into a 3D enclosure. This is by far the most cost-effective method of enclosure manufacturing. Sheet metal fabrication takes advantage of metals’ incredible flexibility and elasticity to its full extent.
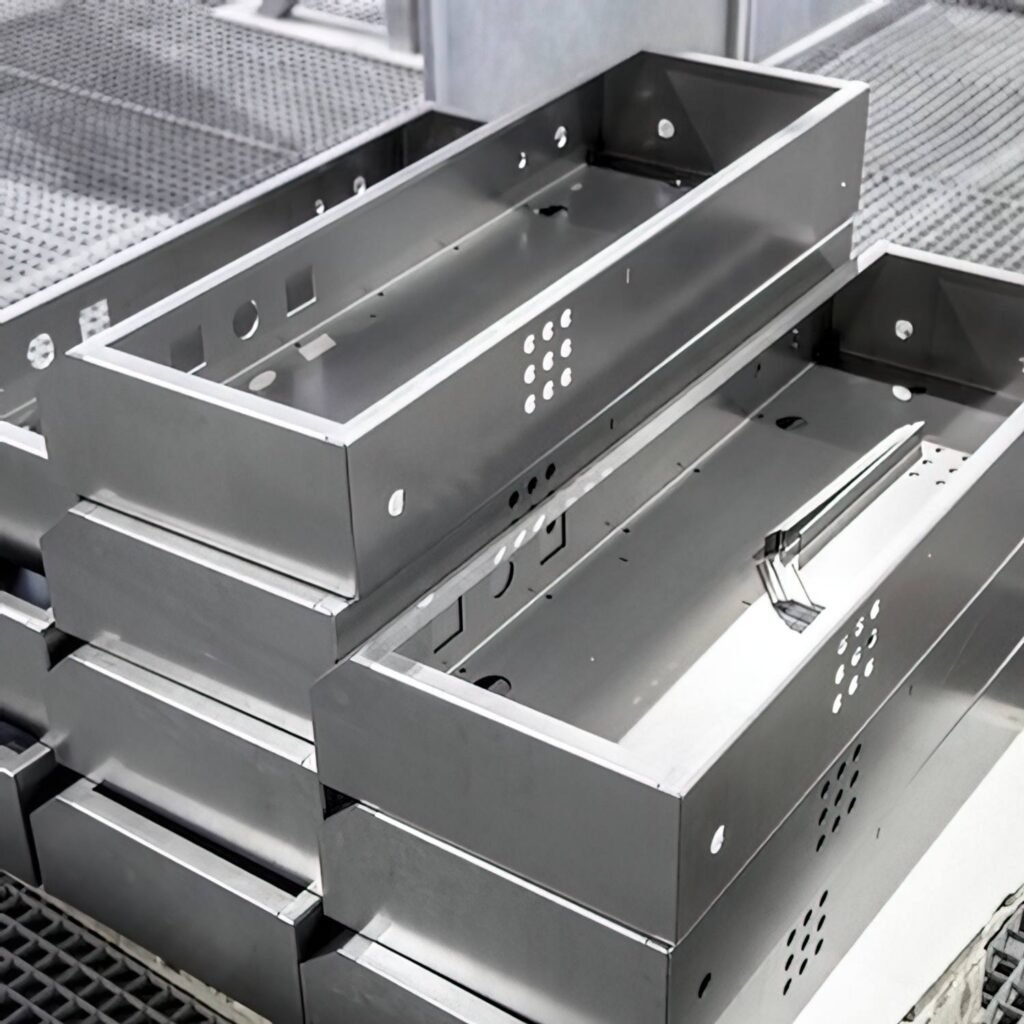
Sheet metal fabrication is limited to ductile metals.
- Injection Molding
Injection molding involves injecting hot molten plastic into a mold. This method is particularly popular because the final enclosures are electrically insulated. Enclosures manufactured through injection molding are relatively cost-effective. The most impactful cost factor in injection molding is the design and fabrication of the mold.
Thus, injection molding will be more expensive than sheet metal fabrication for low-volume productions. But as you increase your production size, the difference shifts in favor of injection molding.
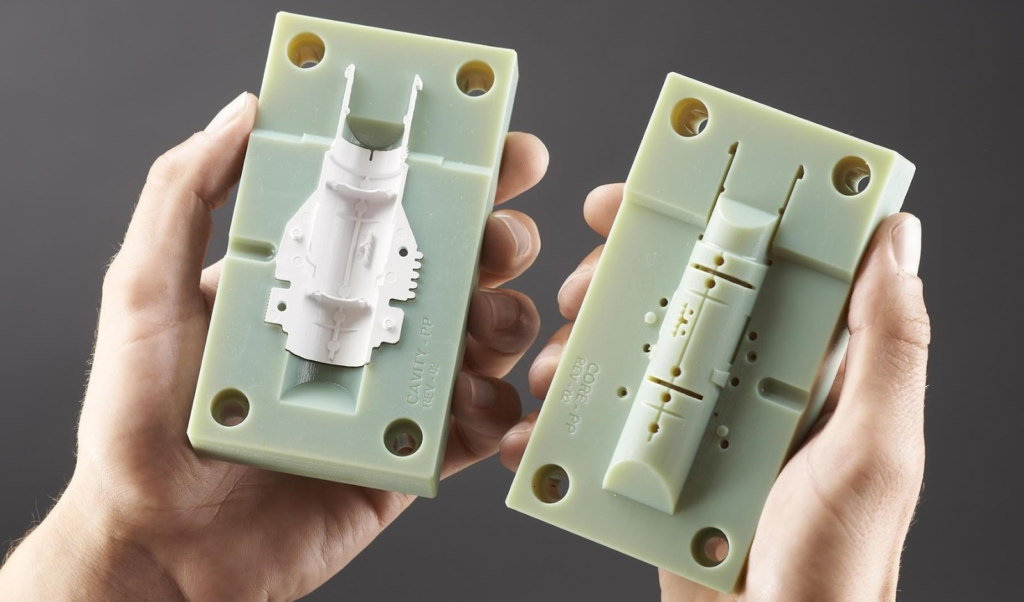
In contrast to sheet metal fabrication, injection molding is limited to plastic materials.
- 3D Printing
The most common type of 3D printing is FDM (Fused Deposition Modeling). Here a wire of plastic (ABS or PLA) is semi-melted and extruded on a base plate. Once the first plastic layer cools another is deposited on top. Thus, FDM creates continuous layers on top of other layers until a finished design is achieved.
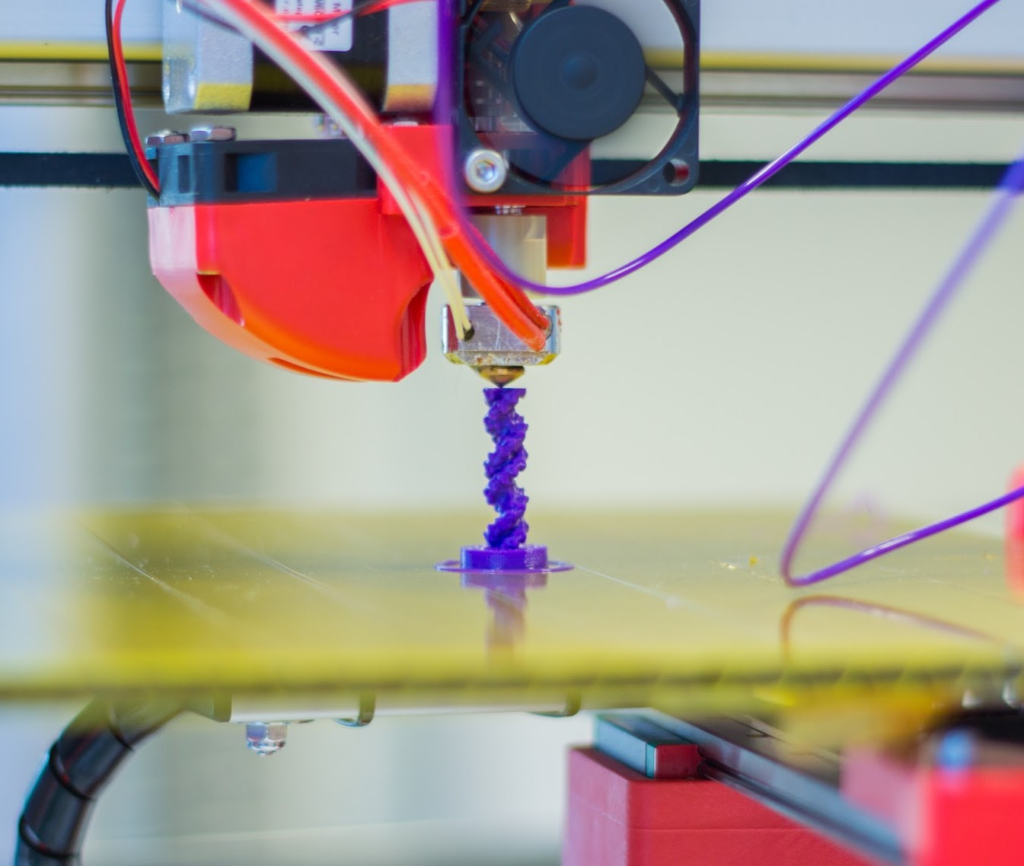
The best part about 3D printing is that it allows users to create the most complex and intricate designs possible. However, 3D printing is a slow and costly process limited to a handful of plastic materials.
- Miscellaneous Manufacturing Techniques
A few more uncommon manufacturing techniques can be used for enclosure production. These techniques have their own shortcomings and are generally not recommended.
Laser Cutting
Laser cutting uses a high-powered laser to make precise cuts into a thin sheet of material.
Laser cutting is a slower process than metal forming. However, it supports both thin metal sheets and slightly thicker wood and acrylic sheets.
Die-Casting
Die-casting is a similar method to injection molding. Instead of a powerful injection of molten plastic, you slowly pour molten metal into a mold.
Die-casting results in more robust products but at a much higher cost.
SLS
SLS, or Selective Laser Sintering, involves a high-powered laser selectively melting metal powder. SLS is 3D printing for metals.
It is the most expensive manufacturing technique on this list. SLS is generally limited to aerospace applications, where cost is less of a factor compared to design and performance.
SLA
SLA or Stereolithography uses a UV light projector to polymerize a resin vat selectively. SLA is 3D printing using a liquid base.
SLA is generally more precise than FDM 3D printing. However, it is not suitable for large-size products.
Following is a simple table discussing the advantages of various manufacturing techniques.
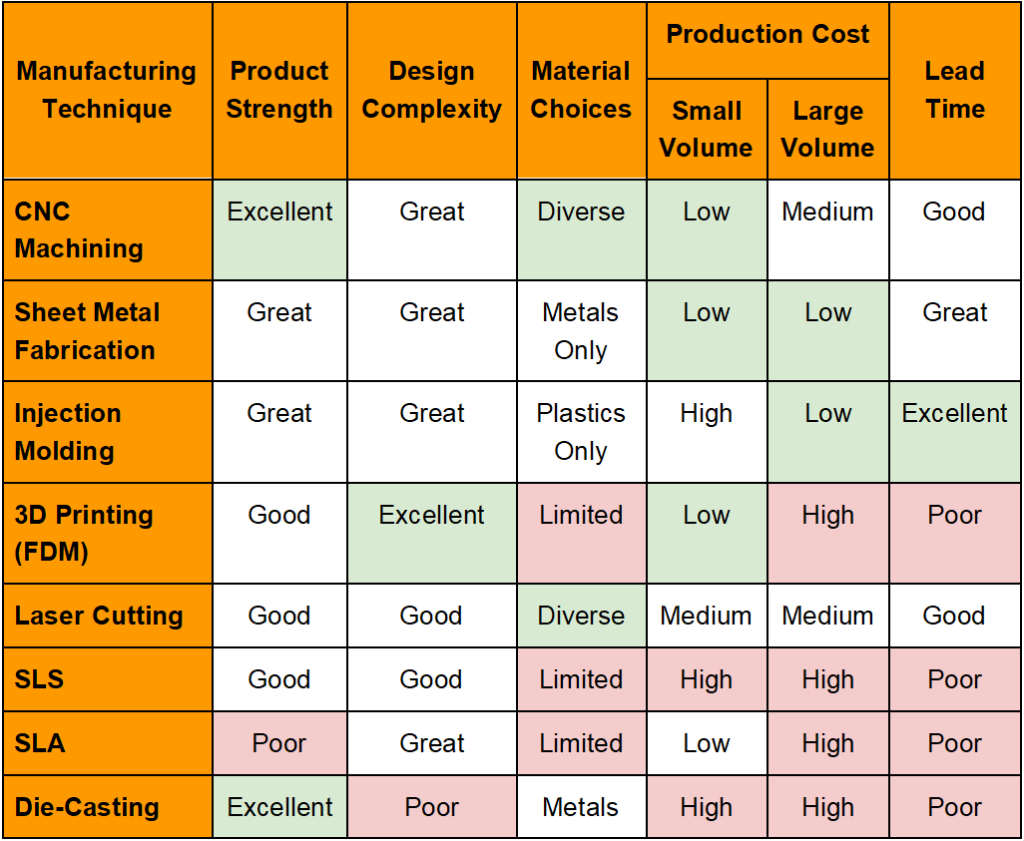
Best Materials for Electronic Enclosures
Metal electronics enclosures are typically made from either Aluminum or Steel. At the same time, non- enclosures can use a variety of plastics.
Steel
Steel is a heavy metal with some exceptional properties. It has a high hardness rating and is still malleable enough to be shaped and formed.
Steel alloys can improve the base properties of steel even further. Depending upon the alloying additive, you can double the corrosion resistance, elasticity, or tensile strength of steel.
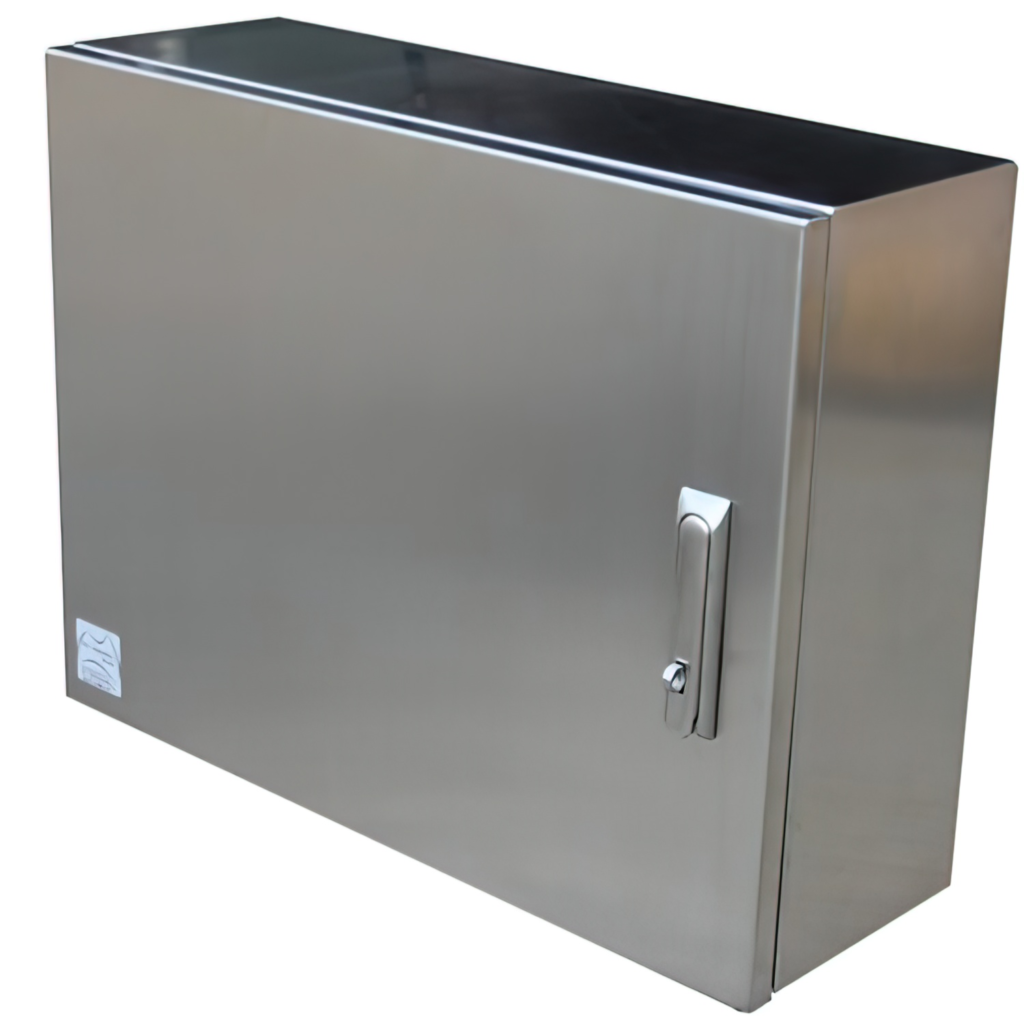
Aluminum
Aluminum is generally lighter and cheaper, while steel is stronger and more expensive. The key benefit of using aluminum is that it is a lighter metal but one that is still fairly strong.
Aluminum alloys are even more versatile than steel alloys. So much so that aluminum alloys are used for both kitchen appliances but also aircraft parts.
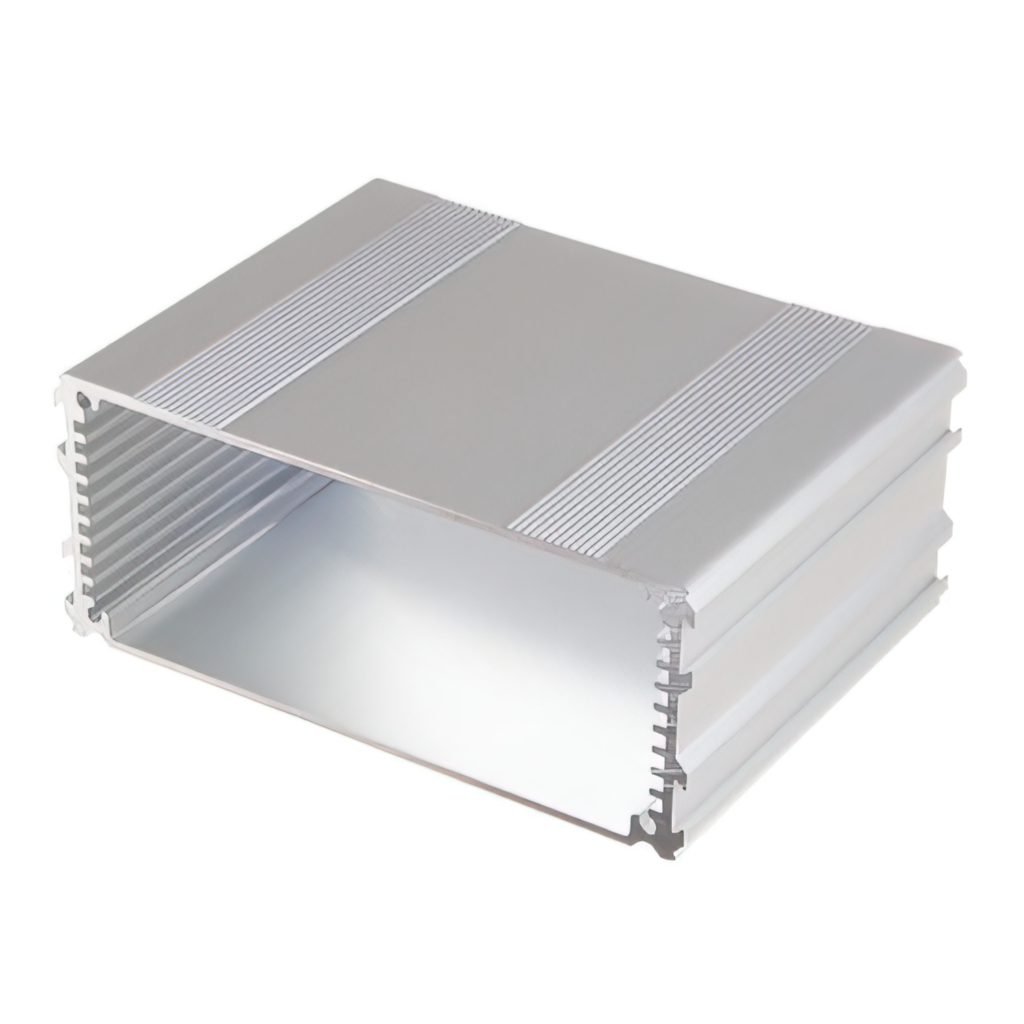
Plastics
Plastics are lightweight materials that are easier to manufacture, resulting in low operating costs. Plastics are a separate industry altogether, using several material bases and even more variations. Some popular plastic options for use in electronics enclosures are as follows.
- PLA & Nylon (3D Printing)
- Thermoset Plastics (Injection Molding)
- Acrylic (Laser Cutting)
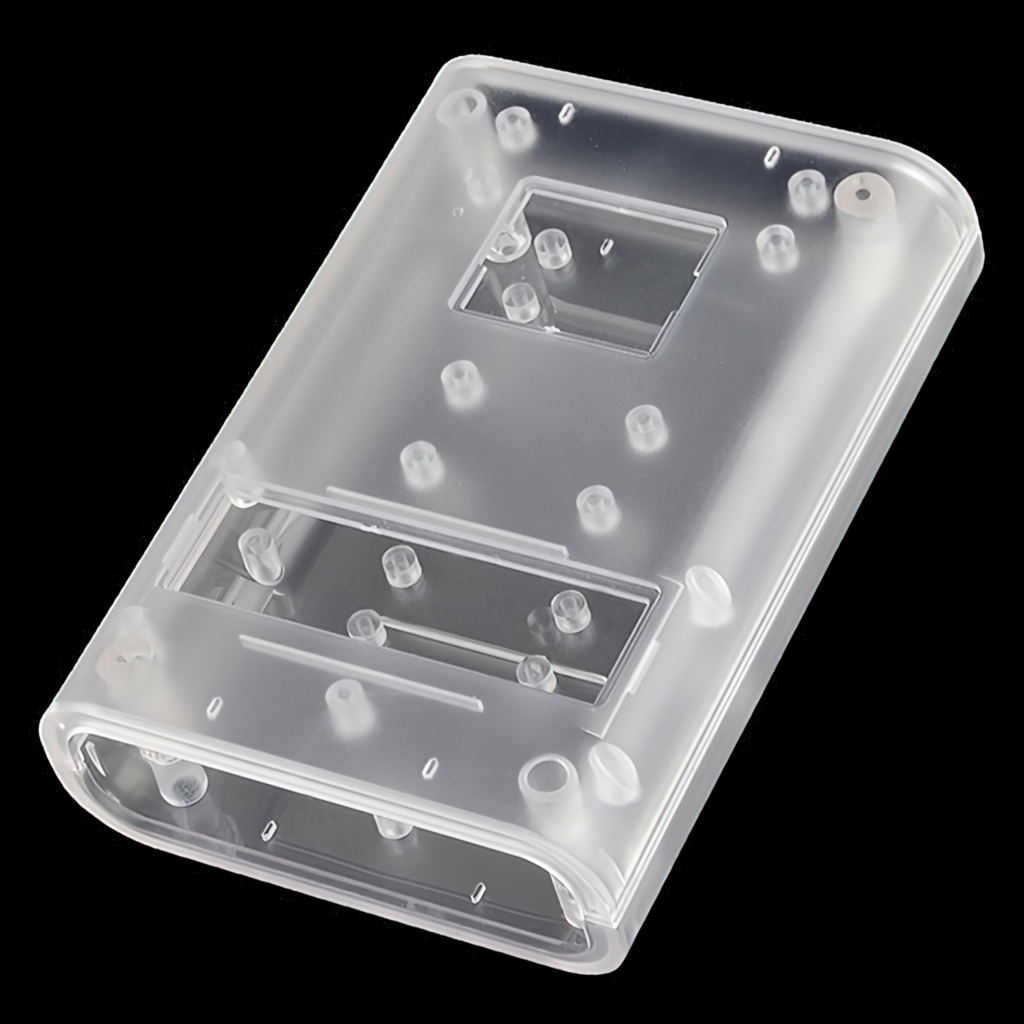
Enclosure Material Comparison
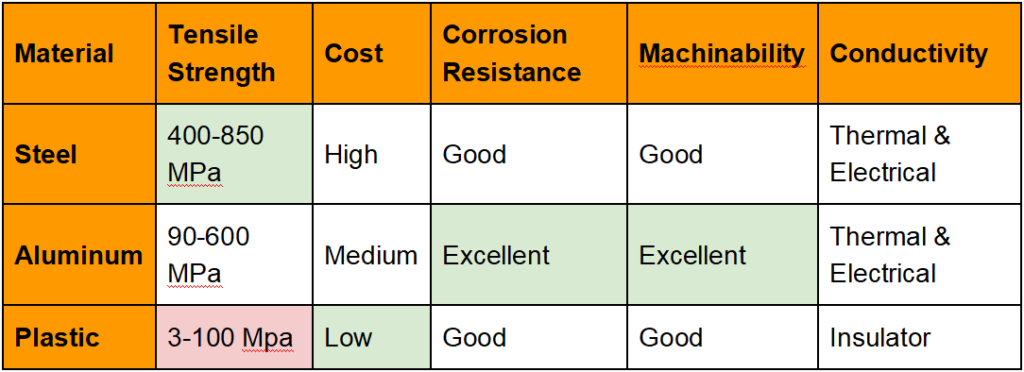
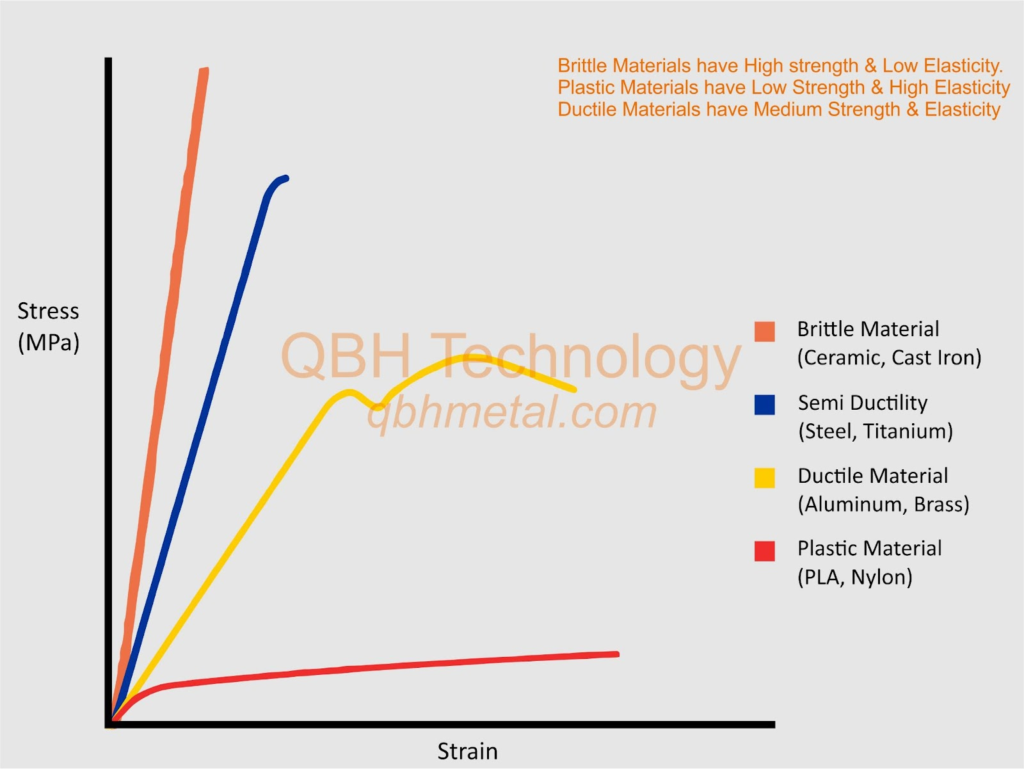
Design Considerations for Electronics Enclosure
Design is generally not a primary factor for most electronics enclosures, but it should not be neglected. We hope you will consider the following design considerations for your electronics enclosures.
Mounting Points
Your electronics enclosure should have proper mounting points built into the design itself. These mounting points can be strategically cut holes or protruding tabs.
Ventilation
Most small electronics can be passively cooled. But for more power heavy electronics, you will need vent holes to allow air to flow. Keep in mind that ventilation holes will be subject to dust and water ingress.
Sealing
For outdoor deployed enclosures, proper water and dust seals are imperative. You can seal your enclosures using gaskets and silicone spacers.
Conclusion
Electronics enclosure seems like a complicated topic at an initial glance. But it becomes quite simple when you know the details. As a general rule, CNC and metal forming are preferred for low-volume metal manufacturing. In contrast, 3D printing is ideal for low-volume plastic enclosures.
For most other enclosure manufacturing, you can balance the financial and time costs according to your needs.
If you are in the market for high-quality manufacturing services, we recommend checking out QBH Technology. We offer an extensive catalog of design, manufacturing, and finishing options.QBH has the best electronic enclosure products in the industry. To get a customized quote and get your business up and running, Contact Us Now!